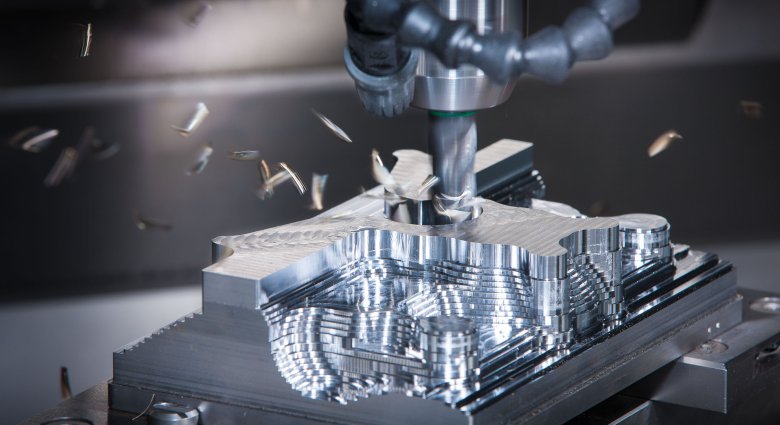
What is grinding of shafts and holes?
Grinding is one of the most common processes in modern industry. This is essential for the manufacture of many products; it is also the final stage in the processing of individual materials. It allows to reduce the roughness of a given surface, as well as to obtain the expected shape and dimensions of the object. Sanding can be carried out on a wide variety of surfaces, both on rollers and on flat surfaces. The tool used to perform this task is a grinder. The most important components of grinding machines are grinding wheels; they are usually made of aluminium oxide and boron, although there are even diamond wheels.
In the case of cylindrical grinding, there are two ways of doing this: longitudinal and transverse grinding. In the first case, the grinding wheel is moved along the shaft, while in the second case, it makes a radial plunge feed, perpendicular to the ground shaft. When sanding shafts, you can also distinguish between fang and centerless sanding.
The grinding of holes is also a very important process for modern industry. There are currently two basic types of kinematic grinding of holes. In the case of the first one, both the wheel and the workpiece perform movements - the feed movement of the wheel and the workpiece rotate. In the case of the second case, the grinding wheel movement is radial feed.
There is also planetary grinding. In its case, the grinding wheel is set in the main rotary motion; this solution is used primarily when it is not possible to set the ground object in motion.
Grinding is a process that has several characteristics. The effect is achieved thanks to the fact that the grinding wheel has a special quern, equipped with sharp edges. They catch on to protruding material scraps, quickly wiping and levelling the entire surface. Sanding should be done properly to avoid potential damage to the material to be sanded. The greatest danger here is caused by the high temperature that arises during this process - it is connected with the high speed at which the grinding wheels rotate. In some cases, this can result in serious structural changes to the sanded workpieces. To avoid this risk, a suitable cooling system must be used to protect the material from damage. However, such a high speed at which the grinding wheels rotate is necessary. If it is too low, scraps of material can get between the individual components and lead to damage. In addition, grinding would not be as effective and accurate if the speed was too low.
Sanding is a very versatile process that can be performed for many different purposes. For this reason, the grinders available on the market today are also very diverse. The most basic are general purpose grinders. Among them there are: claw and centerless grinders, designed for grinding shafts, and grinders for holes - ordinary, planetary and centerless. This group includes also peripheral surface grinders and face grinders.
The second group consists of specialized grinders. This group includes belt grinders, smoothing machines, smoothing machines, smoothing machines and lapping machines. As the name suggests, these devices are used for more specialised activities and are not used in every case. The most advanced devices are those belonging to the group of special grinders. These are mainly cylindrical, valve and valve seat grinders, crankshafts grinders and sharpening grinders.
Sanding is a very common activity, but as you can see, the way it is done and the tools used for it may differ significantly from each other. However, such a great diversity of solutions available here is fully justified. Each material has its own characteristics, and the intended effects of such actions may differ significantly from each other - in each case, it is therefore necessary to apply the appropriate technology.
See more
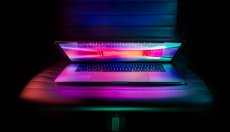
Table under the laptop, what to choose, what to pay attention to?
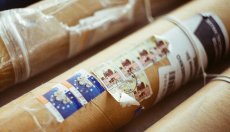
Modern stamps - check out what makes them stand out
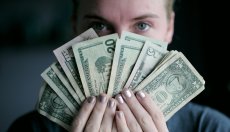